Compression technologies differ in their optimal pressure ranges, and this blog post focuses on the best technologies for the most commonly used range of 6 to 10 bar.
Choosing a compressor – what is best for which application?
Many technologies exist for compressing air, and each technology has its advantages over the rest. Compression technologies include screw, scroll, piston, turbo, and lamellar compression, for example.
OIL-LUBRICATED COMPRESSORS
Advantages of oil-lubricated compressors
- Screw compressors with oil lubrication allow easy heat recovery from the oil or cooling water.
- Compressors with variable-frequency drives allow seamless adjustment. Their efficiency remains high throughout the output profile.
- One screw element can generate up to 13 bar of pressure without intercooling.
In sum, compressor oil holds many advantages.
Downsides of oil-lubricated compressors
- If air quality is critical, compressor oil is the biggest drawback. While compressed air can be treated to contain practically no oil, there is always the risk of oil contaminating the compressed air network when using oil-lubricated compressors. For example, a 75 kW compressor may contain some 35 litres of oil.
- Only the oil separator holds the oil within a compressor. The separator wears down and must be replaced periodically during scheduled maintenance.
- Here there is the risk of receiving and installing a faulty part, which then fails prematurely during operation. The result would be all 35 litres shooting into the network at full blast (e.g. 8 bar). No oil filter can withstand such a load, so in practice, the oil will exit the network at the last point of use.
- The food industry mitigates this risk by using food-grade oils. Although food-grade oils pose no health hazard, such a large volume will be enough to spoil the end product and require cleaning from the compressed air network.
Screw compressors
The most common type of oil-lubricated compressor is the screw compressor. It serves as an excellent “basic machine” for nearly any use. Oil-lubricated screw compressors have several advantages: long service life, good efficiency, low noise, and low price.
Rotary compressors
Based on lamellar compression, the advantages of rotary vane compressors include a very long service life. In fact, rotary compressors last even longer than screw compressors, and in case they seize up, replacing the vane pack is affordable compared to replacing the screw element of a screw compressor.
Rotary compressors are often quieter and smaller than screw compressors. However, rotary compressors lose out in price and efficiency at larger sizes. The best application for rotary compressors is sub-15 kW where compact size and quiet and reliable operation are most important.
Piston compressors
Today, piston compressors are a rare sight in industry. They are recommended by their cheap price but are typically unsuited for continuous operation. They are also expensive to maintain compared to the price of the investment, so they are mainly considered expendable. However, in high-pressure applications (> 15 bar), piston compressors are almost the only option.
OIL-FREE COMPRESSOR TECHNOLOGY
Some technologies need no oil, including scroll compressors, water-lubricated and two-stage screws, and turbocompressors, for example. Some piston compressors are also oil-free, but they are used very rarely.
Oil-free compressors are often expensive, loud, large and heavy; “less-than-user-friendly” compared to oil-lubricated compressors. Naturally, the advantage of oil-free compressors is the complete absence of oil.
Compressor rooms with oil-free compressors are typically clean, and you cannot smell or taste the air as you enter. As a rule, oil-free compressors are the “cleaner” option. This is useful for applications where the machinery is located in workspaces. The mess from oil-lubricated machines is often evident in oil stains on the floor, oily rags around the place, dirt sticking to the oil, etc.
Advantages of oil-free compressors
- Oil-free compressors produce the same amount of oil-free air as any other compressor, but the oil-free compressor does not add to the system’s oil load.
- The risk of oil entering the end product or compressed air network is eliminated completely.
Downsides of oil-free compressors
- The price of oil-free compressors is often about three times that of equivalent oil-lubricated technology.
- It should be noted that oil-free compressors often feed analysis and production equipment worth millions that must not be contaminated in the least. In this case, the price going from €10,000 to €30,000 is hardly significant, as long as it guarantees that the air-powered equipment remains intact.
Scroll compressors
A scroll compressor typically contains one or more 2.5, 5 or 7.5 kW modules. The advantages of scroll compressors include low price, good reliability, low noise, and affordable maintenance.
Their drawbacks are poor efficiency and low module service life. In other words, scroll compressors are a clear winner for applications requiring less than 30 kW of compressor output.
If an application requires some 15 kW of output during normal use, a four-module 30 kW compressor can be used, meaning there are four compressors inside one housing. In normal operation, two generate compressed air while the other two stand by. If one module fails, two can still generate air while one remains on standby.
Scroll compressors require relatively little regular maintenance compared to other technologies. In general, scroll compressor modules are ran to failure and then replaced. The price of a scroll module is typically a fraction of the price of a new screw element.
Water-lubricated screw compressors
If more than 30 kW of output is needed, the price of electricity starts to play a larger role, and the lower consumption of screw compressors beats out the advantages of scroll compressors. Typically, the next step is a water-lubricated screw compressor.
While water- and oil-lubricated screw compressors share some similarities, the obvious difference is their lubricant. The advantages of water-lubricated screw compressors are a good range of adjustment, low noise, and good efficiency. Their service life is mediocre.
The prices of water-lubricated screw compressors land somewhere between scroll and two-stage screw compressors. As a rule, water-lubricated compressors are a good choice for applications between 30 and 75 kW.
Oil-free two-stage screw compressors
For larger applications (> 55 kW), oil-free two-stage screw compressors are the right choice. On one hand, they are often pricy, loud, and less adjustable, but on the other, they offer a long service life and reliable operation. Their efficiency may be very high, depending on the technology used, even higher than oil-lubricated screw compressors.
In recent years, twin-motor compressors with excellent adjustment ranges have entered the market. The maintenance costs of two-stage oil-free screw compressors are roughly on par with oil-lubricated screw compressors, but the initial investment and replacement elements are pricier, of course. However, you should always remember to weigh the risk of oil contaminating the network whenever you price your investments.
Turbocompressors
For very large (> 250 kW) applications, turbocompressors may be the right choice. The advantages of turbocompressors include the best efficiency on the market, extremely reliable technology, and a very long service life.
Typically, turbocompressors have an adjustment range between 30 and 40 per cent, so for a consumption of 50 m3/min, the turbocompressor can adjust by up to 20 m3/min. Turbocompressors are not base load machines, even though many treat them as such.
The initial investment is often expensive with turbocompressors, but increasing a turbocompressor’s capacity from 400 to 600 kW, for example, will not add much to the final price. For comparison, buying two 300 kW two-stage screw compressors is already a more expensive solution than just buying one 600 kW turbocompressor. Once we add the efficiency, lower maintenance costs, and longer service life, it is as clear as day that turbocompressors are the top choice for these capacities.
Turbocompressors must be dimensioned carefully, as there are multiple things to consider. For example, they include intake air temperature, pressure requirements, cooling water temperature, and the needed adjustment range. All of the above affect the compressor’s efficiency, maximum power, number of stages, etc.
Compressed air systems are the sum of their parts
If compressed air is lacking, the answer is not always to buy a new compressor – the system should be viewed as a whole. The Sarlin Syyni compressed air system analysis service gives you accurate measurement data about your system so you can make informed decisions, especially important when you are considering additional capacity. The analysis goes beyond compressors: it covers the entire system’s functionality and air quality as well as pressure levels and their variation.
We are here to help you with compressed air
We have almost 70 years of experience in compressed air and have invested in both technological and service solutions, giving us unrivalled capabilities for helping our customers focus on their core business while improving the reliability and cost efficiency of their compressed air production.
Our customers also have the option to outsource their compressed air production to us, only paying for the compressed air that they consume. We are totally independent of equipment manufacturers, and we service all compressor and dryer brands. Our professional maintenance network covers all of Finland.
Contact us
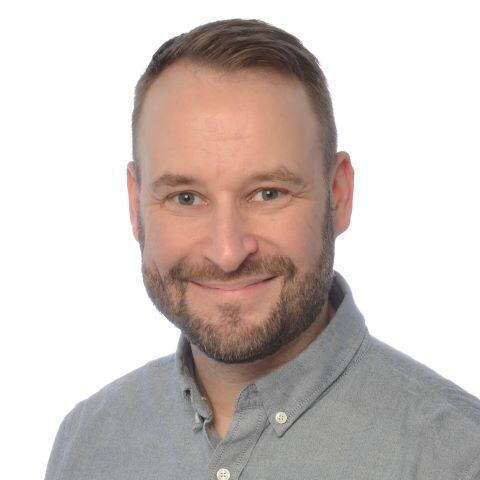
Mika Kiuttu
Key Account Manager, Compressed air
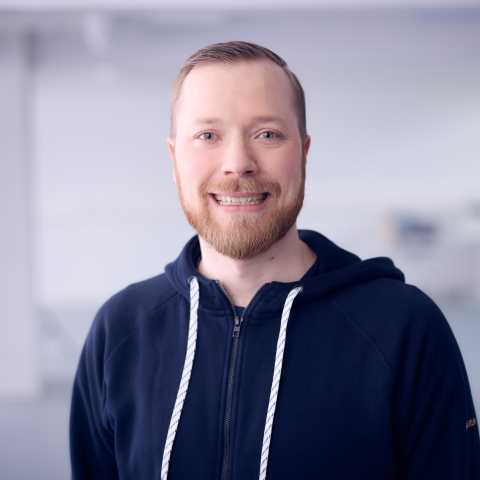
Jesse Suokas
Key Account Manager, Compressed air