In order to understand the basics of secure data transfers, we should go over the principles of the fieldbus and safety bus.
Fieldbus is a communication technology used in industrial automation to distribute digital data between devices and systems. Installing a fieldbus is an easier way of connecting different parts of machinery compared to hardwiring each device separately. Naturally, this makes for a faster and simpler installation process.
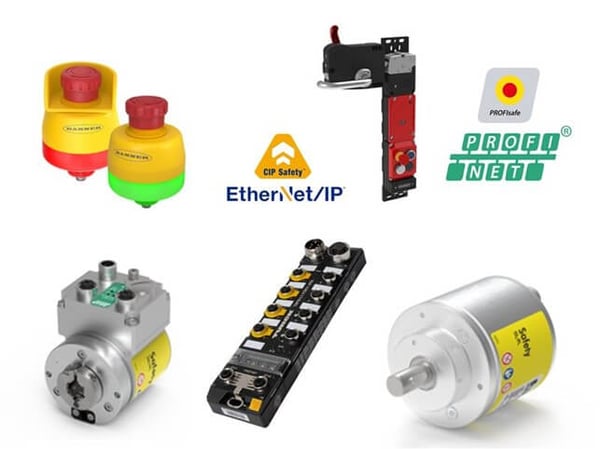
A safety bus is now commonly built inside the fieldbus to facilitate the transfer of machine safety data. As the name suggests, the purpose of the safety bus is to improve the safety of machine controls and management. The design of the safety bus must consider the appropriate and safe ways of using the machine and predict human errors and mechanical breakdowns.
Safety buses have developed by leaps and bounds in recent years. They are now safer, but also much smarter.
Previously, safety buses such as the AS-Interface Safety at Work largely operated with on-off functionality. They could indicate open safety devices but included rather limited sensor data. Typically, one message could only include the safety data of a single sensor, and only four bits at maximum.
Now the question is whether on-off indication is sufficient, or if the customer would like more device data for preventive maintenance and other purposes.
Modern safety buses use Ethernet-based solutions, which allow for many times the detail and volume of useful data. For example, sending fault data and deviations in variables to the control logic allows for accurate preventive maintenance – this type of data is called metadata.
Ethernet itself is not a next-generation technology, but it has been used in recent years to introduce a new dimension to automation. This has increased the versatility, reliability and safety of sensor solutions.